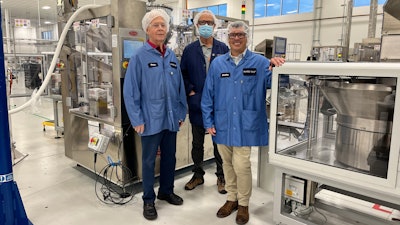
Cosmetics giant Mary Kay’s Lewisville, Texas facility contains 20 packaging lines that serve the company's whole gamut of cosmetics products, from creams and lotions to colognes and lipsticks.
Industry equipment veteran George Bode, now manager of corporate engineering, joined the company in 2016 with more than two decades of cosmetics experience at L’Oreal already under his belt. One of his early assignments in 2018 was to open the then new Lewisville greenfield operation and move a deep existing installed base of packaging equipment to the facility.
But as the equipment was transported and refitted at the new location, a tube and carton line for mascara and lip balm products was noticeably scant in automation sophistication compared to others. Mascara in particular is more difficult to automate than most other tubes—more on why that is later.
With only a filler and some conveyance, mascara packaging operations at the facility had been quite manual until 2022, requiring 12 to 14 operators on three different shifts to keep the line running. The company made it work with people power for a few years, but people became scarce, necessitation temp agencies. When the pandemic hit, the labor-intensive operation became untenable—managing 36 to 42 temporary workers through COVID-19 was a heavy lift. Bode saw automation as a way to remove the company from an unending treadmill of hiring, training, rehiring, and retraining.
Scarcity and turnover weren’t the only labor issues; the cost of labor was also going up. Temp service prices spiked during the pandemic, making the decision to automate a simple math problem based on ROI. The finance department provided Bode with the year-to-date temp hours spent on the mascara line, specifically on the filling equipment. A simple cost-benefit analysis revealed a quick payback on automation, potentially two years or less.
“That was the tipping point,” Bode says. “This [summer 2023 mascara and lip balm line] is the first new packaging line that we’ve done since 2015 or 2016.”Brush, wand, and cap assemblies enter the filling and closing monoblock.
Unique set of equipment needs
The mascara line would need to accommodate six to eight different primary and secondary packaging formats, all in 4-g fill to 8-g fill tubes, and in 2.5-in to 4-in tall cartons. That might seem like a modest number of formats, but each of the eight comes in dozens of different “flavors” (formulas, colors, viscosities). That makes for a lot of SKUs, and in turn, a lot of changeover.
The frequency of changeover on the mascara line would precipitate a shift away from Mary Kay’s existing, highly sophisticated attitude toward automation. Other recent packaging lines projects consisted of continuous-motion machines that operated from 120 up to 150 pieces/min. But for a few reasons, that level of automation seemed unrealistic for the mascara line.Individual caps ready to be torqued onto filled bottles.
First, the equipment itself was almost as expensive as labor, eating into the favorable payback timeframe. To get the ROI and payback they sought, the company hoped to land at about half to even a third of the cost of its high-speed continuous lines.
On top of that, the Lewisville operations staff has never been highly trained technically—few operations groups contain mechanics or engineers. In that labor environment, changeovers on sophisticated equipment takes time, taking longer to debug the machines between runs, and longer to ramp them up to operating speeds.
So instead of the fastest continuous-motion equipment, “we tried to stay within that 50 to 60 pieces/min range with intermittent equipment,” Bode says. “It’s less sophisticated than the continuous lines. Of course, it’s sound equipment—everything is servo, including the feeder bowls. But the difference is they’re feeder bowls in the first place, as opposed to vision-guided robotics. But the tradeoff isn’t just price, it also means it’s much easier to change over. A big reason that’s important to us is that we have a lot of SKUs, and a lot of smaller work order sizes.”
A starwheel orients tubes for filling.
Also, as is the case across the cosmetics space, gentle handling was a requirement. These are prestige products that use luxe, sleek packaging in many cases. Scuffed tubes or smudged inks are sore spots for cosmetics manufactures. Specific to mascara, equipment that bends application brush and wand is a dealbreaker.
Other musts for new equipment included a minimum speed to justify automation in the first place, and temp force reduction—both variables in the equation could yield a two-year payback. Bode was going to have to thread a needle between sophistication, flexibility, speed, and ease-of-use.
Vendor selection
With these constraints in mind, Bode and his team set about to finding equipment to fill the bill. Longtime acquaintance and PallayPack local representative Richard Talbot of Equip-Pak suggested TGM, an Italian manufacturer known for operating in the cosmetics space. That led Bode to another acquaintance, PallayPack, an OEM that serves as the North American office for TGM alongside several other global OEMs.Rotary filling of mascara tubes.
“I have a policy not to build anything I can buy,” says Louis Pallay, PallayPack president. “Everything we build, from gummy lines to vial filling and vaccine manufacturing equipment, those are all built in Montreal. But for our customer Mary Kay, for this specific application, bringing in TGM was the correct choice.”
Bode and Brandon Polyniak, Mary Kay’s reliability manager, travelled to PallayPack in Montreal and TGM in Italy for other CPGs’ integrated tube line FATs. Seeing the full lines in action sealed the deal for Bode.
Purpose-built among several parties
The multi-party OEM, integrator, and brand owner partnership worked as follows. PallayPack asked Mary Kay for a highly specific user requirements (URS) document from which to work. Based on those requirements, TGM would deliver a turn-key line consisting largely of TGM equipment. Once the non-disclosure was signed, Mary Kay would write all the POs to PallayPack. The company dealt with importing the machinery, ordering spare parts, and deploying North America service technicians, “although we really haven't needed a lot of service yet,” Bode says. Notably, Mary Kay requested a modem be installed on the system for remote access from afar, greatly assisting in troubleshooting.
The brush and wand extend so far beyond the closure collar that, when the cap is closed over the tube just after filling, the brush is plunged deep into the product well under the closure.
“From the time the equipment hit the dock, we uncrated, installed, powered-up, and then TGM came in set everything up debugged, and we were running finished goods in that 28-day window.”
“PallayPack and TGM worked with us closely to make sure we got what we wanted,” Polyniak adds. “He was careful about making sure we got exactly what we needed, knowing what our requirements were, and the line was turn-key. We had some certain options that we wanted to keep standardized, like inkjet printers, for instance, because that’s what our people are familiar with, and they accommodated that… It was just nice to go to one place to qualify this equipment.”
“Even though their cost, relative to the project, is considerably less than some of the continuous-motion options, it is first-rate equipment,” adds Bode. Servo controllers on the system.
, for the last five or six months, we’re averaging 60% to 70% uptimes even with the frequent changeovers. And sometimes we’re doing much better than that.”
According to Pallay, who reminds Bode that the machine is specified for 50 pieces/min, not 50 to 60, it might be a little too efficient. He spoke of seeing 100% OEE figures on his last visit to the Lewisville location.
“How do you get a line that runs at 100% OEE? You buy a line that’s supposed to go at 50 a minute, and you run it at 55 a minute,” jokes Pallay. “That was one of the things that we asked them not to do, but they’re hitting record productivity numbers.”
Not to get lost in the equipment’s performance or efficiency has been the headcount of temp workers it obviated. Mascara production on the old filling line required 12 to 14 people. The new automated line needs only two operators.
Unique mascara tube construction
Packaging mascara is more complex than filling and closing most other tube cosmetics products. Like other tubes, like the lip balms that also run on this line, a mascara primary packaging consists of two elements. One half of the pack is a tube that acts as a well to hold the somewhat viscous liquid product. On the other half of the package is a cap or closure that is threaded or otherwise affixed over the tube well below to contain the product within.
But in the case of mascara, a brush at the end of a wand is affixed to the interior of the tube-shaped closure, joined under the circular closure top and extending down the center of the cylindrical closure, protruding beyond the closure collar. Consumers use this brush to apply the mascara. The brush and wand extend so far beyond the closure collar that, when the cap is closed over the tube just after filling, the brush is plunged deep into the product well under the closure. This means that the brush is loaded with the viscous mascara product when it’s first closed after filling, and again whenever a consumer unscrews the cap and applies mascara.
Fully assembled mascara tubes are checkweighed immediately upon exiting the filling block.
.” Bode says. “The brush that goes in the mascara is a delicate silicone fiber, and it would not successfully run on the other automated machine—hence the reason for this being a more manual operation until recently. PallayPack and TGM looked at the brush and said, ‘no problem.’”
The tube container that acts as a product well has its own unique feature as well—a valve called a wiper that is inserted into the tube neck after filling, but prior to closing with the brush and closure. This wiper carefully controls the amount of product that’s allowed to exit the product well on the brush. As a consumer opens the tube, the device gently wipes excess product away from the brush as it slides upwards through the neck and removed from the well. The wiper valve ensures that product dosing is consistent for the consumer, use after use.
All in all, mascara packaging has a few extra components that lip balm or lip gloss doesn’t, making automation tricky.
The new packaging line
The new mascara line begins with tandem TGM bulk feeder bowls, each feeding a TGM filler. Each feeder introduces one half of the tube and closure combination to the filling module.
The first hopper to the right of the filler introduces the empty tubes that are to be filled with mascara product. From a 45-deg incline conveyor, the hopper feeds the empty tubes into a vibratory feeder bowl from Bonino Group that sorts and single-files the tubes into conveyance that carries the tubes horizontally into the filler. The tube could be oriented with either neck leading, or the heel leading. There, an eight-slotted star wheel accepts the continuous infeed of tubes and indexes them, orienting them vertically into an intermittent servo-based rotary filler.
“
The dial-table in the filler is a 16-puck system that intermittently deliver tubes to a filling nozzle that precisely doses product formula into the tubes. In parallel, and within the filling enclosure, an unscrambler and sorter single files the wiper features and feeds them intermittently into another star wheel, indexing them for application. A servo-based arm with pneumatic gripper picks wipers from the wheel and applies to the necks of tubes, immediately after filling, while they’re still resting in their respective puck on the dial table.
“A lot of lines have pucks that carry these products, especially a tall cylindrical product,” Bode says. “The only pucks related to this line are inside the filler, actually in the dial table that rotates the empty bottles around for filling and adding the wiper.”
Circular bottom labels are applied after a 90-degree turn orients the tubes from end-to-end, to side-by-side. On-tube and on-label coding and marking is done in the stage.
Literature or pamphlets are pulled from a magazine (upper right), then using belts, are shot (lower left corner) to a position between the tubes and the erected cartons. When a pusher pushed the tube into the carton, the pamphlet comes along for the ride, enveloping the tube entirely within the carton.
“The cosmetic industry is really prone to overfill and giving away formula,” Bode says. “While they’re not as expensive as, say, vaccines, it's still rather expensive to be giving it away. The checkweigher has been a real advantage in keeping us from giving away extra formula.”
The green belt shoots the literature or pamphlet in between the carton and the mascara tube. When tubes are pushed into the carton, the literature goes along for the ride.
receives a code on the tube heel; either a pre-printed pressure sensitive label, or an inkjet code that’s printed onto a blank label.
Cartoning operations follow labeling. Three in-line servo-based robotic arms simultaneously pick and place individual tubes into waiting TGM cartoner infeed buckets at the handshake between the labeler and cartoner. Meanwhile, within the cartoner, a servo-based arm picks flat, printed, pre-glued 2D carton blanks from a magazine and erects them. Pamphlets (Mary Kay refers to them as literature) are pulled from another magazine, and belts shoot it into a stationary waiting position between the carton and the tube. When the tube is pushed into the open carton, it hits the center of literature, which folds around the tube and travels with it into the carton cavity.
Carton coding with a laser coder.
Bottom carton flaps are closed mechanically with locking tabs rather than adhesive, and the mascara tubes are pushed into the open cartons, which are similarly closed thereafter.
The cartons are then laser coded on a Hitachi laser printer. Laser coding is used for the high print quality and the cleanliness compared to inkjet methods. This practice reduces ink as a consumable input and ensures cleaner cartons. Also, many of the cartons have a slick, glossy finish that doesn’t accept ink as easily—ink could be wiped off prior to drying. The cartons are coded with lot, batch, and date information on the carton closure flap.
After coding, cartons make another 90-deg turn to the right, this time retaining their side-by-side orientation. They are accumulated in this orientation until a Keyence photo eye recognizes a 24-count layer. The completed 24-count layer is then lowered to accommodate another 24-count layer, which will be pushed on top of the preceding layer in a down-stacking operation.
The first layer of 24 cartoned mascara tubes drops to make room the second layer. Once the 10th layer is added, a 240-ct cubic block is formed.
After 10 layers are stacked, a 24 by 10 cube of cartons, or 240 count, is oriented for side-load case packing in corrugated cases. The cases are erected by servo-based robotic arms, with bottoms closed first with tape. The 240-count product cube is then pushed, side loaded into the awaiting corrugated case.
The 240-ct cube of cartoned mascara tubes is pushed or side loaded into a waiting erected case.
What’s next?
It’s not always the case that slowing down a packaging line leads to greater productivity, but in the era of SKU proliferation and frequent changeovers, there’s a place for it.Side-load case packing happens after the case is erected and bottom flaps are tapled closed. Once packed with 240 cartons, the top flaps are closed and the finished cases leave the line. Palletizing is manual at this pace.
“This is the direction we're going,” Bode says. “We've actually got another line starting later this year, and we’re sourcing that with the same companies because we like their equipment. And we're going to stay within those slower speed ranges, with intermittent motion below 80 pieces a minute. We’re staying in the indexing equipment because it has worked so well for us.”
As for the existing mascara, Polyniak is also impressed. “You can tell they put a lot of thought into how everything works, and attention to detail,” he said. PW